Mezzanine floors can be constructed to support heavy-duty operations, including the use of industrial machinery. The structures can also provide additional storage if needed.
When it comes to building a mezzanine in any scenario, it must be fit for purpose so that it is not only structurally sound but also complies with all applicable health and safety or building regulations. However, with heavy-duty use, there can be more regulations to comply with compared with an mezzanine used for lighter purposes such as office or employee break room.
If you work with us here at The Mezzanine Company, we will conduct a detailed survey to ensure your mezzanine floor meets all of the necessary requirements.
In the meantime, here is an overview of some of the top things to consider when building a mezzanine floor to support heavy machinery or storage.
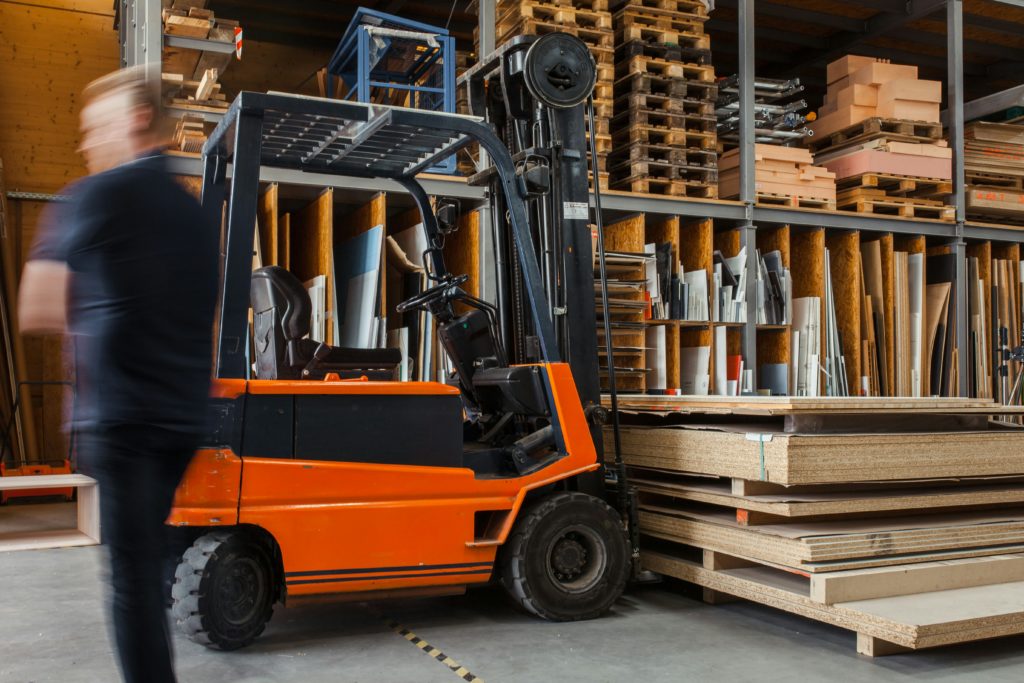
Load-Bearing Capacity
As the name suggests, the load-bearing capacity of a floor refers to the load the floor can safely support. Typically, this is measured in square metres i.e. kN/m² or kg/m².
Every mezzanine floor must be built to a specific load-bearing capacity. However, the required ratings can look very different depending on the usage intentions of the mezzanine floor.
Here are a few example scenarios:
Offices: 2.5 – 3.5 kN/m² (250–350 kg/m²)
Light storage: 4.8 – 5.0 kN/m² (480–500 kg/m²)
Heavy storage: 7.2 – 10 kN/m² (720–1000 kg/m²)
Heavy machinery: 10 – 20+ kN/m² (1000–2000+ kg/m²)
Vehicle or forklift traffic: 15+ kN/m² (requires custom engineering)
The exact load-bearing requirements will be determined following a structural survey. However, the above still gives an idea of how the usage requirements of a mezzanine floor can impact the level of load-bearing capacity needed.
While supporting heavy machinery or storage is certainly possible with a mezzanine floor, it must be built to be able to safely withstand the increased loads.
The load capacity itself will also vary depending on the span between supports, beam material, beam size, decking type and point loads.
Discover: Our industrial mezzanine floor services

Structural Design
Beyond ensuring the mezzanine floor has the required load-bearing capacity, the rest of the mezzanine floor itself will need to be built so that it can maintain heavy-duty activity. This is not just in terms of the physical weight of the load, but also other practical elements including the noise and vibrations created.
For example, decking options could include structural steel or concrete on metal decking. Such materials are better equipped to withstand heavy machinery, and can also provide anti-vibration properties.
Additionally, the floor must be a material that minimises the risk of slips and trips. In industrial settings where spills may occur, the surface should not only be anti-slip but also easy to clean.
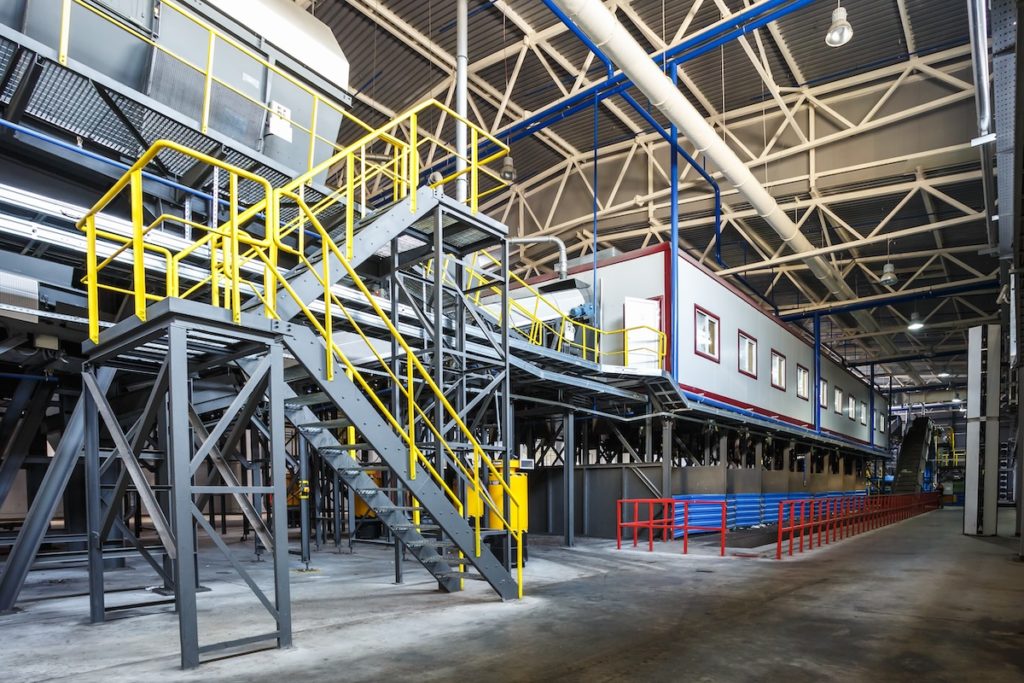
Safety Access
Mezzanine floors must allow for the safe movement of people, equipment and materials.
When installing a mezzanine floor for heavy machinery and storage, some adaptations may be needed to ensure all safety requirements are met.
Examples of safety regulations which may apply to a mezzanine floor include:
- BS 5395 (Stair design) and BS EN ISO 14122 (Machinery access systems)
- BS 9999
- BS EN 12464-1
- BS EN ISO 14122-4
- Building Regs Part B
- Building Regs Part K
- Lifting Operations and Lifting Equipment Regulations (LOLER) 1998
- The Building Regulations 2010 (Part K, M, B)
- The Health and Safety at Work Act 1974
- The Workplace (Health, Safety and Welfare) Regulations 1992
The aspects of the mezzanine floor which require safety access considerations include staircases, guardrails, toe boards, pallet gates, walkways, hoists, lifts and handrails.
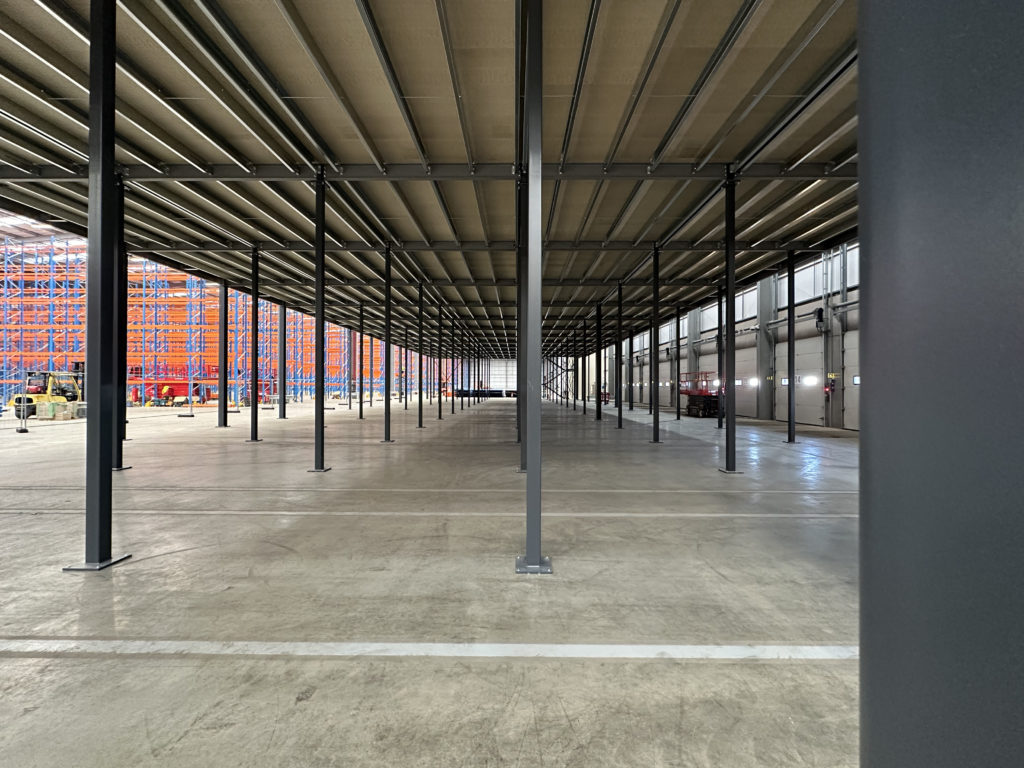
Fire Rated Compliance
If a mezzanine floor will house 3 or more people at any one time and exceeds 20 metres in length, then it will also need to be built as a fire rated mezzanine. Although this post is about all things mezzanine floors for heavy materials or storage, fire rated regulations apply regardless of the usage purpose of the structure.
When a mezzanine does need to be fire rated, it will need to be constructed in a way to resist the spread of fire for a fixed duration, i.e. 30, 60 or 90 minutes.
It will contain aspects such as fire protection to structural steel, fire rated soffits, fire rated ceilings underneath, enclosed stairs, escape routes, smoke detectors, sprinkler systems, emergency lighting and signage.
You may also be interested in: Does Your Mezzanine Floor Need To Be Fire Rated?
Get A Mezzanine Floor For Heavy-Duty Industrial Use In The UK
When designing and installing a mezzanine floor for heavy-duty machinery and storage, it’s challenging to cover everything in a blog post alone.
But, when you work with us, our mezzanine experts will cover all bases to ensure the mezzanine will be structurally safe and sound. Also, that your mezzanine floor will fully meet the commercial needs of your business.
If you are in search of a mezzanine floor to provide additional space for your operations, then please get in touch with us today. From there, we can provide tailored information and arrange a survey of your building.
The Mezzanine Company is based in Nottingham, and our team covers a wide radius across Nottinghamshire, Leicestershire, West Yorkshire and South Yorkshire.
Alternatively, please give us a call on 0115 939 7572 to speak to our friendly team.